Returns logistics: returns management is emerging as a strategic issue
In November 2023, Amazon integrated the ReturnGo returns management platform into its Multi-Channel Fulfillment service, enabling third-party sellers to automate and optimize their reverse logistics.
ReturnGo, which processes more than 250,000 returns a month, offers customers a returns and exchange portal integrated with online sellers' stores. It can connect to any existing carrier and has a growing network of warehouses and drop-off points, according to its website.
Using ReturnGo will help sellers "deliver an automated, simple and easy-to-use returns experience for their customers", said Wain Yu, director of Multi-Channel Fulfillment at Amazon, in a statement.
In the dynamic world of modern commerce and in the age of online shopping, where simplicity of purchase is often key, returns management is emerging as a strategic issue, often downplayed. Well-orchestrated returns logistics are not just a way of dealing with returned products, but an opportunity to boost customer satisfaction and make your business more sustainable. In this article, we explore returns logistics, addressing the challenges, benefits and best practices for ensuring quality after-sales service.
The challenges of supply chain returns management
As consumer expectations evolve and companies seek to optimize their operations, returns management is a crucial challenge, exposing companies to operational complexities. Challenges include the need to process returns quickly to maintain customer satisfaction, the management of defective or damaged products, and logistics coordination to ensure the efficient flow of returned items. These obstacles, which are often interconnected, underline the importance of a holistic and proactive approach to ensuring efficient and satisfactory returns management.
Among these challenges, the costs associated with inefficient returns management have a direct financial implication. The costs of transporting, handling and repairing damaged products can quickly degrade a company's overall profitability. Moreover, returns that are not effectively managed can result in lost revenue, particularly if returned products cannot be put back into stock or are depreciated.
These often underestimated costs underline the strategic importance of implementing effective returns management processes to mitigate these financial impacts and preserve the economic health of the business.
The different types of returns in the Supply Chain
Comprendre les nuances des différents types de retours est nécessaire pour mettre en place des stratégies adaptées et efficaces. Voici une liste des principaux types de retours en Supply Chain.
Understanding the nuances of different types of returns is essential to implementing appropriate and effective strategies. Here is a list of the main types of returns in the Supply Chain.
- Returns for refund
These returns occur when customers want a full refund on a product. This can be due to a variety of reasons, such as unsatisfied expectations, changes of mind or quality issues. Managing these returns requires a clear refund policy and transparent procedures to ensure customer satisfaction while minimizing losses.
- Product exchanges
Product exchanges are frequent, especially when customers receive an item that does not meet their expectations or has minor defects. Efficient returns logistics must enable fast, worry-free exchanges, ensuring that customers quickly receive the correct product, thus reinforcing satisfaction and loyalty.
- Seasonal returns
Some industries experience seasonal returns, particularly after periods of high sales activity such as the festive season. Managing these returns often involves large volumes, and requires advance planning to avoid any major disruption to the supply chain. Temporary warehouses and a flexible workforce can be solutions to manage these seasonal peaks.
- Returns for repair
Some products may be returned not because they are faulty, but because they require repair or adjustment. Implementing an efficient returns process ensures that products are quickly repaired and returned to customers, minimizing inconvenience.
- Returns of out-of-date or obsolete products
In some sectors, such as food or electronics, returns of out-of-date or obsolete products are unavoidable. Managing these returns requires precise coordination to avoid any significant financial loss. Liquidation strategies, responsible recycling or reallocation of these products may be options to consider.
- Returns due to ordering errors
Order errors, whether on the part of the customer or the supplier, can lead to returns. Putting in place effective processes to identify, rectify and avoid these errors helps maintain operational efficiency while preserving customer satisfaction.
- Returns of damaged or defective products
Apart from scheduled returns, damaged or defective products are inevitable. Managing these returns requires careful inspection, transparent communication with the customer, efficient processes to minimize losses and restore customer confidence.
By understanding these different types of returns, companies can adapt their policies and processes to respond effectively to the different needs of their customers, while maintaining fluid and efficient returns logistics within the supply chain. Flexibility and responsiveness become key assets for any company seeking to excel in Supply Chain returns management.
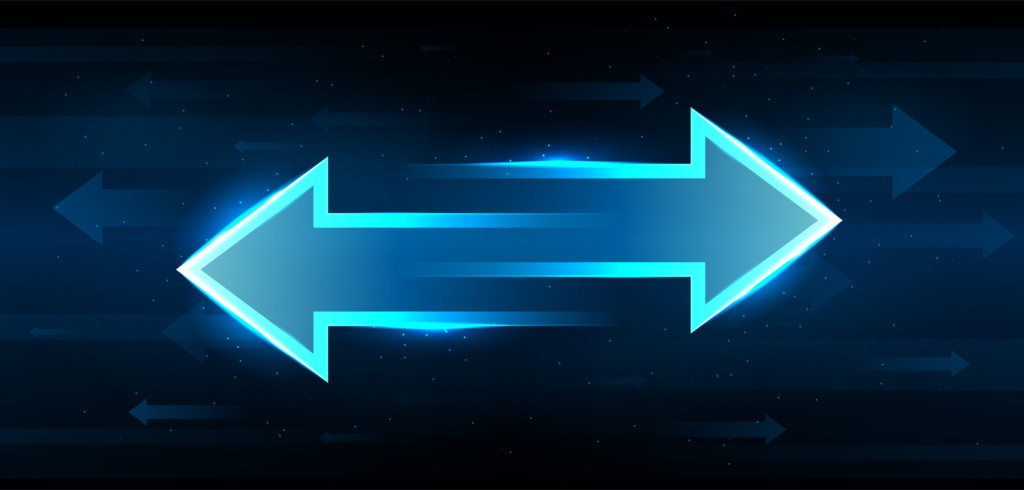
Best practices for cost-effective returns management
Developing transparent and easily accessible returns policies is a key element in ensuring customer satisfaction. By providing clear instructions on return times, conditions and processes, you eliminate ambiguities and build customer confidence throughout the returns process.
Implementing a robust returns tracking system is another pillar of this approach. By providing greater visibility at every stage of the process, this transparency facilitates planning and resource management, enabling a rapid and effective response to ongoing returns.
The integration of detailed inspection protocols is crucial to thoroughly assess the condition of returned products. This helps to differentiate reusable items from those requiring repair or disposal, ensuring appropriate inventory and returns management.
The creation of specific storage areas according to the condition of returned products (new, damaged, repairable) simplifies returns management by avoiding confusion and optimizing storage space.
At the same time, establishing solid partnerships with reliable logistics providers is also essential. Transparent communication and close coordination with these partners facilitate efficient returns processing while keeping costs under control.
A thorough analysis of the costs associated with returns, including transport, repair and management costs, is vital. This helps identify opportunities for optimization and cost reduction.
Finally, proper training of personnel involved in the returns management process ensures consistent execution of policies and procedures, minimizing errors and delays.
Here are some practical tips for optimizing your returns process!
Adopting a continuous improvement approach by regularly soliciting feedback, both from customers and from employees involved in returns management, enables to constantly adjust and optimize practices, thus contributing to an even more satisfying customer experience.
Simplify returns initiation by offering user-friendly online options, making the process as easy as a few clicks. Make it even easier by providing prepaid return labels, easing the administrative workload for customers.
Offer maximum flexibility by allowing in-store returns, providing a convenient option tailored to customer preferences. Encourage substitution rather than refunds to promote product recovery while meeting changing customer needs.
Enhance the returns experience by presenting attractive incentives, such as discounts or coupons, encouraging customers to choose returns over abandonment. And reinforce customer loyalty by introducing programs specifically linked to returns, demonstrating your commitment to a long-term relationship with your customers. In short, an integrated approach to these strategies will help create an efficient returns flow that benefits the customer and is profitable for your business.
Assessing the effectiveness of returns management is as crucial as the process itself, and relies on carefully selected key performance indicators (KPIs). The "returns rate" offers a global perspective by measuring the percentage of items sold that are returned, providing a basis for assessing the frequency of returns. "Returns processing time" is an essential KPI, measuring the speed with which returned products are processed, directly influencing customer satisfaction. Meanwhile, "product recovery rate" assesses the proportion of returned items that can be returned to stock or reused, offering insight into the financial viability of the returns process.
Strategic use of data is also essential to identify areas for improvement. Analysis of the reasons for returns, such as recurring defects or shipping errors, guides the necessary adjustments in the supply chain.
Data on return costs helps assess the efficiency of logistics processes, while analysis of returns by product or customer segment enables management strategies to be customized.
In summary, the judicious combination of relevant KPIs and in-depth data analysis provides a comprehensive view of returns logistics performance, enabling companies to optimize their processes and boost customer satisfaction.
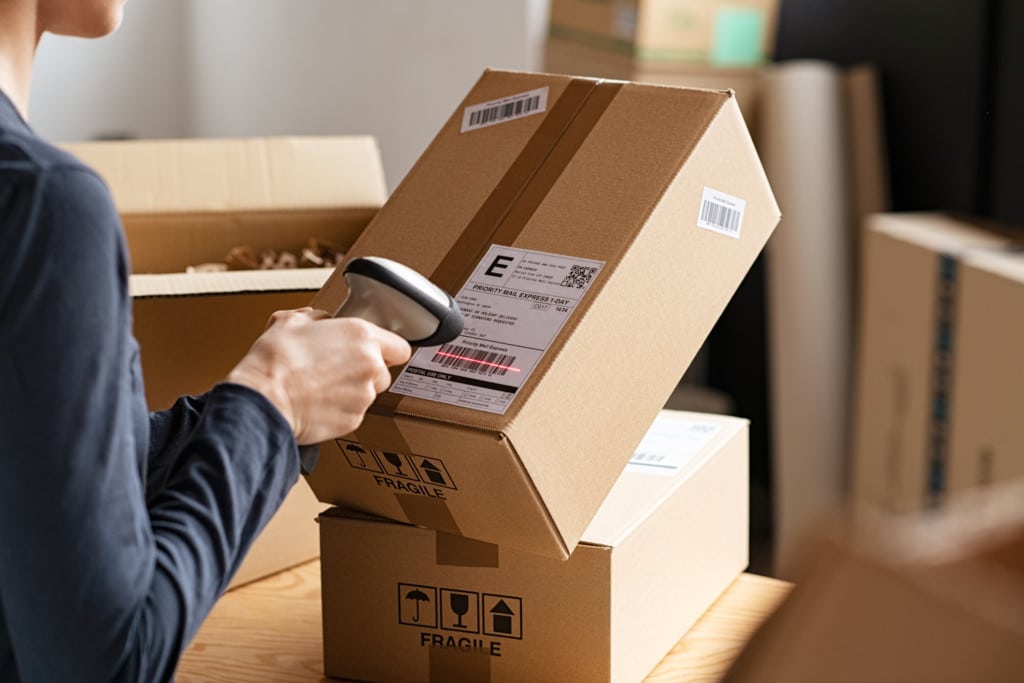
Conclusion
In conclusion, the management of returns is not just an unavoidable, restrictive step, but a strategic opportunity in the modern supply chain. By meeting the challenges with well thought-out logistics, returns become a major lever for building customer loyalty, reducing costs, and strengthening brand reputation.
The diversity of returns demands constant adaptability. Transparent policies, accurate tracking, detailed inspection, targeted storage areas, strong partnerships, rigorous cost analysis, effective training and a culture of continuous improvement are all key elements.
In short, well-orchestrated returns management is not only necessary, it's transformative. It pushes the supply chain towards operational excellence, perpetuates the company's reputation, and places customer satisfaction at the heart of its strategy.