MPS and supply chain: what can a master production plan do for you?
The Master Production Schedule (MPS) is a cornerstone of modern supply chain management. It serves as a strategic framework for planning production activities, enabling production capacities to be aligned with customer demand. By integrating sales forecasts, market analyses and historical data, MPS provides a clear vision of short- and medium-term production requirements. This vision is crucial to ensuring that resources are used optimally, helping to reduce production costs, improve customer satisfaction, and minimize the risk of supply/demand mismatches.
Based on reliable data, a MPS enables companies to react quickly to market fluctuations. For example, if a company sees a sudden increase in demand for a specific product, the MPS can be adjusted to increase production of that product, while decreasing production of other products that are less in demand. This not only maximizes revenues, but also strengthens the company's competitive position.
MPS, a pillar of supply chain performance
MPS plays an essential role in overall supply chain performance. It is often described as the heart of production planning, as it integrates customer requirements with company capacities. In this context, MPS is both a management tool and a communication document. By establishing a clear, structured plan, it enables all the departments concerned – production, logistics, sales and finance – to work in synergy towards common goals.
The importance of MPS also lies in its ability to enhance predictability. By enabling the company to plan its activities proactively, MPS helps to reduce interruptions in the production process. When production teams know what they need to produce and when, they can better anticipate raw material, labor and equipment requirements. This not only reduces the costs associated with emergencies and delays, but also improves the quality of the final product, as each stage of the process is carefully coordinated.
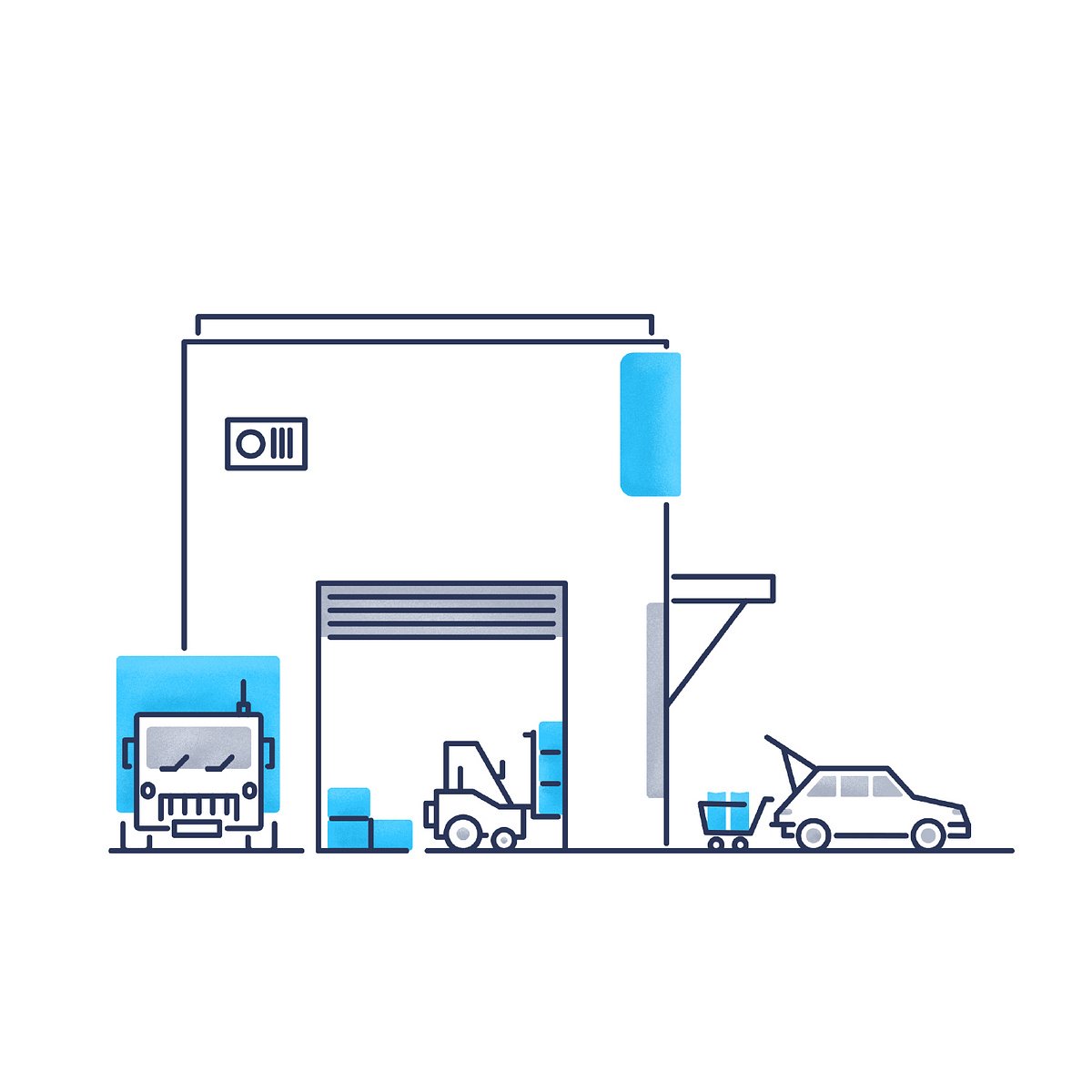
Demand management and Master Production Schedule in supply chain
Demand management is intrinsically linked to MPS, as it relies on the ability to predict fluctuations in market demand. This requires in-depth analysis of historical trends, consumer behavior, and external influences such as seasonality or marketing campaigns. An effective MPS leverages these analyses to produce accurate demand forecasts that guide production.
A crucial aspect of this management is the balance between supply and demand. A well-designed MPS not only reacts to changes in demand, but also anticipates future needs. For example, if a company anticipates an increase in demand for a product during a specific season, it can adjust its MPS accordingly, increasing production and planning raw material purchases upstream. This avoids shortages and ensures that the company is able to meet customer needs without building up excessive inventories.
Another important point is the interconnection between demand management and other elements of the supply chain, such as inventory management and logistics. By integrating these different dimensions, MPS contributes to a holistic vision that optimizes the whole system, enabling operations to run more smoothly.
What is a supply chain MPS?
The Master Production Schedule, or MPS, is a strategic framework that defines what needs to be produced, in what quantities, and when. It is based on a careful analysis of sales data, production capacities, stock levels and delivery times. PDP is more than just a production schedule; it's a complex management tool that requires a thorough understanding of the company's operations.
To develop an effective MPS, it is essential to collect accurate data on past demand, and use it to predict future needs. This involves the use of advanced analysis tools and forecasting software that can process large volumes of data and identify significant trends. Once forecasts have been established, it is crucial to evaluate existing production capacities. This includes analyzing available resources, such as manpower, machinery and raw materials, to ensure that the company can meet demand forecasts.
The MPS must also be aligned with the company's strategic objectives. This means that MPS decisions must support the company's overall vision, whether this involves increasing market share, improving profitability, or developing new products.
MPS and Supply Chain: what can a master production plan do for you?
MPS is central to supply chain management for a number of reasons. Firstly, it ensures alignment between the company's various departments. By establishing a clear production plan, MPS facilitates communication and collaboration between production, logistics, marketing and sales. Each department understands how its activities fit into the overall process.
What's more, MPS promotes proactive planning, which is essential in a dynamic business environment. By analyzing market trends and forecasting variations in demand, MPS enables the company to adapt quickly. For example, if a company identifies an upward trend in demand for a product, it can adjust its MPS to increase production before this demand becomes fully apparent.
Another important aspect of MPS is its role in resource optimization. By enabling precise planning of production activities, MPS helps minimize the costs associated with over- or under-production. This not only reduces inventory costs, but also improves the utilization of human and material resources.
Join the ranks of the companies we have helped.
Contact us to find out how we can achieve the same results for you.
How to develop an effective Master Production Schedule (MPS)?
Developing an effective Master Production Schedule (MPS) requires a methodical and structured approach. First, it is essential to start with a thorough analysis of demand data. This involves collecting historical sales data and using analytical tools to identify patterns and trends. By integrating external data, such as economic information and industry trends, companies can refine their forecasts and develop a more comprehensive understanding of future needs.
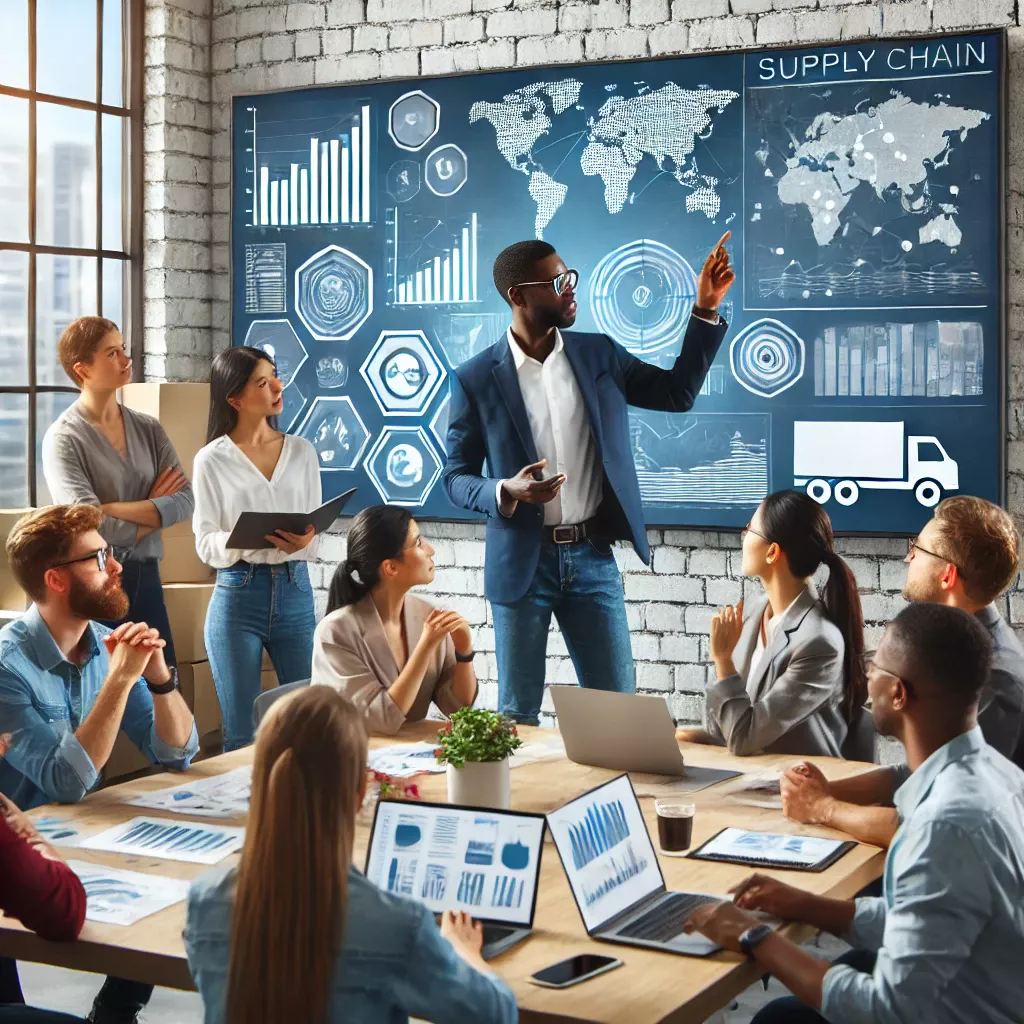
Once demand forecasts are established, it is crucial to assess production capacities. This requires an analysis of available resources, including equipment, labor, and raw materials. This evaluation helps identify potential constraints that could limit production, allowing for adjustments to the Master Production Schedule (MPS) accordingly. The development of the MPS itself should be a collaborative process involving all stakeholders. Production, logistics, sales, and finance teams should be involved from the beginning to ensure that the plan meets everyone's needs. This also allows for the quick identification and resolution of any potential conflicts or issues.
Once the MPS is developed, it is important to establish monitoring and reevaluation mechanisms. The market evolves rapidly, and an MPS must be flexible enough to adapt to these changes. This involves implementing key performance indicators to assess the effectiveness of the plan and to make real-time adjustments if necessary.
What are the key steps to implementing a successful Master Production Schedule (MPS)?
- Implementing a successful Master Production Schedule (MPS) requires following several critical steps. The first step is to clearly define production objectives. These objectives should be aligned with the company's overall strategy and take into account customer expectations, market trends, and internal capabilities.
- Next, data collection and analysis are essential. This involves not only examining historical sales but also analyzing external factors that could influence demand, such as promotions or changes in consumer preferences. Once the data is analyzed, it is crucial to develop scenarios based on these forecasts, considering various variables that could affect production.
- Once the Master Production Schedule (MPS) is in place, communication with all stakeholders is essential. It is important that each department understands its role and responsibilities in the implementation of the MPS. Regular meetings and updates are necessary to ensure that all teams are aligned and that the MPS is executed effectively.
- Finally, regular monitoring and evaluation of the MPS are crucial to ensure its success. This involves measuring results against forecasts and making adjustments based on actual performance. A company that adopts a proactive approach in managing its MPS is better positioned to adapt to market changes and meet its customers' needs.
What are the advantages of a well-executed Master Production Schedule (MPS) for a company?
A well-executed Master Production Schedule (MPS) offers several significant advantages for a company. First, it helps improve customer satisfaction. By ensuring that products are available at the right time and in sufficient quantities, a company can respond quickly to customer demands, thereby strengthening their loyalty and trust.
Additionally, an effective MPS reduces costs. By optimizing resource utilization and minimizing excess production, a company can achieve substantial savings. This not only results in lower inventory costs but also leads to better allocation of human and material resources.
Finally, a well-designed MPS enables the company to be more flexible. In a constantly evolving business environment, the ability to adapt quickly to changes in demand is crucial. An effective MPS allows companies to pivot swiftly and seize new opportunities, whether by launching new products or adjusting production in response to market fluctuations.
Quelles sont les différences entre le PDP et d'autres concepts similaires tels que le MRP (Materials Requirement Planning) ou le MPS (Master Production Schedule) ?
It is important to understand the distinctions between the Master Production Schedule (MPS) and other planning tools, such as Material Requirements Planning (MRP) and Production Planning (PDP). The PDP focuses on overall production planning, integrating demand forecasts and production capacities to establish a coherent production plan. It is, therefore, a long-term vision that guides all operations.
In contrast, MRP is more centered on managing the materials needed for production. Its primary goal is to ensure that the necessary raw materials and components are available at the right time to support the production process. MRP focuses on the operational level, ensuring that the materials required for production are in place without creating excess.
The MPS, on the other hand, specifically focuses on the production of finished products. It provides a detailed schedule indicating when each product should be manufactured, taking into account demand forecasts and production capacities. The MPS can be seen as a derivative of the PDP, concentrating on the operational detail level to ensure efficient production.
mps supply chain
How to integrate the Master Production Schedule (MPS) with other elements of the supply chain, such as inventory management and demand planning?
Integrating the Master Production Schedule (MPS) with other elements of the supply chain is essential to ensure maximum efficiency. This requires a collaborative approach where all departments work together towards common goals. For example, sales teams can provide insights into market trends that may influence demand forecasts, while production teams can offer feedback on actual capacities and constraints.
It is also crucial to use technological tools to facilitate this integration. ERP (Enterprise Resource Planning) systems are particularly helpful as they allow for data centralization and ensure smooth communication between different departments. These systems can help synchronize information related to production, sales, and inventory management, ensuring that all stakeholders have the most up-to-date information.
Finally, adopting a dynamic approach is essential. The market is rapidly evolving, and the MPS must be flexible enough to adapt to changes. This involves implementing feedback mechanisms that enable teams to quickly respond to new information and adjust the MPS accordingly.
mps supply chain
What software or tools are available to facilitate the creation and management of a Master Production Schedule (MPS)?
The creation and management of a Master Production Schedule (MPS) can be greatly facilitated by the use of various software and tools. ERP systems, for example, allow for the integration of different business functions, thereby simplifying resource planning and management. These systems centralize data, providing better visibility across the entire supply chain.
Other specialized production management tools, such as production management systems, offer advanced features to help plan and track production activities. These systems enable efficient resource management, real-time tracking of production performance, and quick identification of bottlenecks. Demand forecasting tools are also essential for developing an effective MPS. By using advanced algorithms and predictive models, these tools can analyze large volumes of data to produce accurate forecasts. This allows companies to better anticipate future needs and adjust their production plans accordingly.
How to manage changes and necessary adjustments in a Master Production Schedule (MPS) during execution?
Managing changes in an MPS during execution is a critical aspect of production planning. In a dynamic business environment, the MPS must be adaptable. To achieve this, companies need to implement monitoring systems that allow them to track the MPS's performance in real time against forecasts. This monitoring must be accompanied by organizational flexibility. Production teams must be ready to quickly adjust their activities in response to new information, whether it's an unexpected increase in demand or production issues. Open communication between departments is essential to ensure that all relevant stakeholders are informed of changes and can adapt accordingly.
Furthermore, continuous staff training plays a crucial role in managing adjustments. Teams must be familiar with the tools and processes required to effectively make changes to the MPS. This can include regular training sessions on the software used, as well as updates on best practices for production planning and management.
mps supply chain
How to measure and evaluate the effectiveness of a Master Production Schedule (MPS)?
The evaluation of the effectiveness of a Master Production Schedule (MPS) relies on the use of key performance indicators (KPIs) that measure results against the set objectives. Among these KPIs, the customer satisfaction rate is an essential indicator, as it reflects the company's ability to meet customer expectations in terms of delivery times and product quality.
Furthermore, production cost analysis is another crucial indicator. By comparing actual costs to forecasts, companies can identify discrepancies and determine the underlying causes. This can reveal inefficiencies in the production process, enabling improvements.
Inventory levels are also a key indicator of MPS effectiveness. Closely monitoring inventory levels ensures they align with demand forecasts and production plans. By tracking these levels, a company can avoid overstocking or stockouts, thus ensuring optimal resource management.