Can we say that in the pharmaceutical industry, supply chain processes are simple, but that the complexity lies in compliance with GxP standards?
Each industry has its own Supply Chain specificities. These specificities are structuring: they have an impact on tools, organizations and processes. These specificities are diverse: distribution networks, type of storage, degree of warehouse automation, levels of partner integration, etc. These specificities can be linked to the market, the product, geographical constraints, and other more or less determining factors.
Regulation is a major source of specificities for the Supply Chain. It is in the pharmaceutical industry that we can observe the most structuring specificities originating from regulation. In this article, we propose to present the GxP regulation and its main impacts on the Supply Chain. We will describe some of the solutions that we believe are most suitable to meet the Supply Chain expectations of this regulation. Finally, we will propose a roadmap to implement or upgrade your GxP Supply Chain.
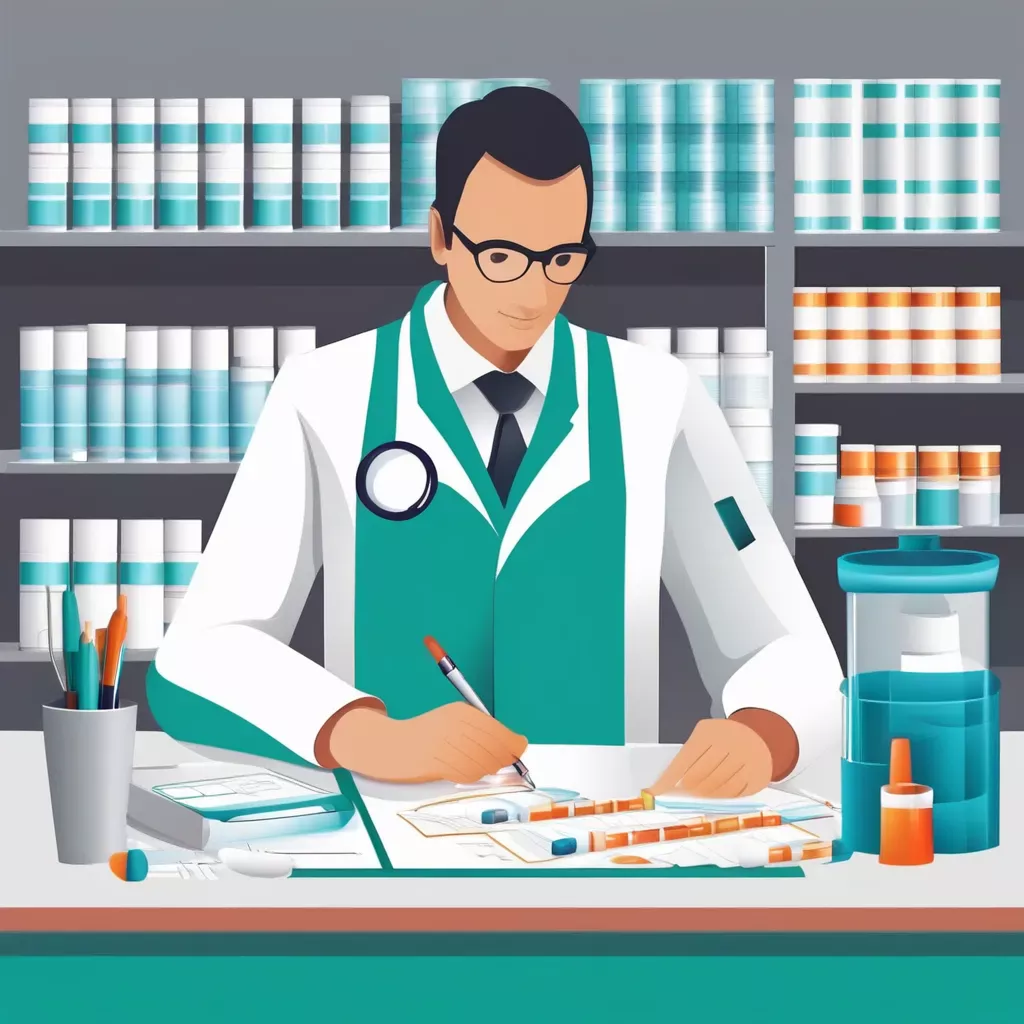
Key figures
The transport of pharmaceutical products is a crucial sector, especially with the rise of vaccines and biological therapies. In 2023, the volume of pharmaceutical transport is estimated to be in billions of dollars value, with a strong predominance of air transport for products requiring strict cold chain management. Estimates vary, but figures show that more than 50 million tons of pharmaceuticals were transported around the world in 2023.
The global pharmaceutical industry is made up of thousands of players, including large pharmaceutical groups, biotechs, contract research organizations (CROs), contract manufacturers, as well as distributors. It is estimated that there are more than 20,000 pharmaceutical companies in the world, including multinationals and small businesses. In terms of employment, the pharmaceutical sector employs several million people around the world. In 2022, around 5 million people worked directly in the global pharmaceutical industry.
Perimeter
The Supply Chain is a world of its own. It would be too long and too imprecise to consider the entire Supply Chain to decry the impacts of the GxP regulation on its operation. We propose to limit the scope of this article to the Supply Chain of a pharmaceutical production site based in Europe. This site would be restocked by its suppliers for 90% of the flows in an external warehouse. For the rest of the 10%, the site would be restocked directly in its own warehouse. The site has its own analysis laboratory and uses its storage provider as a sampling site. A single production line would be connected to the site’s warehouse. The site would store the 3 temperatures: ambient, cold and frozen.
What is GxP regulation?
The GxP regulation refers to a set of guidelines and good practices used in the pharmaceutical, biotechnology and medical device sectors to ensure the quality, safety and efficacy of products. The “G” in GxP refers to “Good”, while “x” is a wildcard character that can refer to different types of practices depending on the specific context. Here are the 2 types of practices that have the most impact on our Supply Chain:
GMP (Good Manufacturing Practice): These rules ensure that products are manufactured in a consistent and controlled manner, in accordance with the appropriate quality standards for their intended use and in accordance with the conditions of the marketing authorization.
GDP (Good Distribution Practice): These practices govern the distribution of medicines to ensure that they are handled correctly throughout the supply chain, preserving their quality and integrity.
Compliance with GxP regulations is crucial for healthcare companies, as it ensures that products are safe for patients and meet international regulatory requirements. In addition, these practices minimize the risk of errors, contamination, or failures, which is essential to protect public health.
GxP regulations are widely adopted internationally. The GxP principles are used as a reference by many regulators and standards bodies around the world, allowing for some harmonization of practices in the pharmaceutical, biotechnology, and medical device industries. However, there are regional and national variations in the implementation and enforcement of these standards.
a. Examples of International and National Regulations
- EMA (European Medicines Agency): In Europe, the EMA applies GxP guidelines to ensure the quality, safety and efficacy of pharmaceutical products. Regulations are harmonized across the Member States of the European Union.
- FDA (Food and Drug Administration): In the United States, the FDA imposes GxP regulations, especially GMP. FDA standards are often considered a global benchmark, but they may differ from those in other regions.
- PMDA (Pharmaceuticals and Medical Devices Agency): In Japan, the PMDA applies similar GxP regulations, but with particularities specific to the Japanese market.
- WHO (World Health Organization): The WHO publishes GxP guidelines that serve as a reference for developing countries and for companies wishing to obtain WHO prequalification for their products.
- Swissmedic is the Switzerland Therapeutic Products Regulatory Authority responsible for the implementation and supervision of GxP regulations in Switzerland. Swissmedic works closely with EU regulatory agencies, such as the EMA, to harmonise standards and practices.
b. Harmonization and Divergences
Although GxP regulations are international in nature, their application may vary depending on local jurisdictions. Companies operating internationally must therefore be aware of regional specificities while respecting the fundamental principles of GxP.
c. Standards Development
GxP standards are defined by a combination of international organizations, national regulatory agencies, and standards bodies, with strong collaboration between the different actors to ensure global harmonization.
GxP standards are typically developed through a collaborative process involving public consultations, expert committees, and regular revisions to incorporate scientific and technological advances as well as new regulatory requirements. Once developed, these standards are adopted by national regulatory agencies and must be followed by pharmaceutical, biotechnology, and medical device companies.
d. International Organizations
- ICH (International Council for Harmonisation of Technical Requirements for Pharmaceuticals for Human Use): ICH is an organization that brings together regulatory authorities and the pharmaceutical industry from the main regions of the world (United States, Europe, Japan). It develops harmonized guidelines for the quality, safety and efficacy of medicines, including GxP standards.
- WHO (World Health Organization): The WHO develops guidelines, especially for developing countries, on Good Manufacturing Practices (GMP) and other GxP practices. These guidelines are often used as a global reference.
PIC/S (Pharmaceutical Inspection Co-operation Scheme): It is an international organization that aims to harmonize GMP standards around the world by facilitating cooperation between regulatory agencies. The PIC/S guidelines are adopted by many countries.
e. Standards Organizations
ISO (International Organization for Standardization): ISO develops international standards for various industries, including quality (ISO 9001), that influence GxP practices, although they are not specific to the pharmaceutical sector.
USP (United States Pharmacopeia): USP sets quality standards for drugs and pharmaceutical ingredients, influencing GMP practices.
f. Pharmaceutical Industry
Industry Associations: Associations such as the European Federation of Pharmaceutical Industries and Associations (EFPIA) in Europe, and the Pharmaceutical Research and Manufacturers of America (PhRMA) in the United States, participate in the development of standards by collaborating with regulatory agencies and international organizations.
Join the ranks of successful businesses we’ve helped.
Get in touch to learn how we can achieve the same results for you!
Applying GxP Standards to Other Industries
Although GxP standards are most commonly associated with the pharmaceutical industry, they are also applied in a variety of other industries where product quality, safety, and efficacy are critical. These standards ensure that products are manufactured, tested, and distributed in a way that protects public health and meets strict regulatory requirements.
Manufacturers of medical devices, from surgical instruments to medical imaging equipment, apply Good Manufacturing Practices (GMP) to ensure the safety and reliability of their products. Although the food and beverage industry mainly uses Good Hygiene Practices (GHPs) and Good Manufacturing Practices (GMPs), some GxP standards can be applied, especially in the manufacture of dietary supplements, active pharmaceutical ingredients (APIs) used in food, and medical foods. Cosmetic companies that make products with health claims or are close to the pharmaceutical category often follow Good Manufacturing Practices (GMP) to ensure the safety and quality of their products. In the chemical sectors, especially those involved in the production of intermediates for the pharmaceutical industry, Good Laboratory Practice (GLP) is often used to ensure compliance with safety and quality standards.
Contract research organizations (CROs) that conduct clinical trials or preclinical studies on behalf of pharmaceutical companies follow GxP standards to ensure the validity and reliability of the data.
Examples of GxP rules
Change control is a systematic procedure put in place to manage any changes to manufacturing processes, equipment, raw materials, or documentation. The goal is to ensure that any changes do not negatively affect the quality of the final product. Change control is essential to maintaining quality and compliance in manufacturing processes. Without rigorous change management, there is a risk that uncontrolled changes could compromise the safety or efficacy of a product, leading to quality issues, product recalls, or regulatory non-compliance.
This rule applies in many contexts, for example when changing a production recipe for a drug, when installing new equipment in a production line, or when changing the specifications of a raw material.
As another example, effective document and archive management is crucial to ensure compliance with Good Manufacturing Practices (GMP). Proper documentation ensures the traceability of activities, transparency of operations, and the ability to trace problems or errors for corrective and preventive actions. All procedural documents, such as standard operating procedures (SOPs), work instructions (WIs), and quality policies, should be created and reviewed in a systematic manner. Procedures must be documented in a clear and precise manner to ensure that they are understandable and applicable by the personnel concerned. Documents should be regularly reviewed and updated to reflect changes in practices, regulations, or audit results. Revisions must be documented, including the date of the revision, the changes made, and the persons responsible.
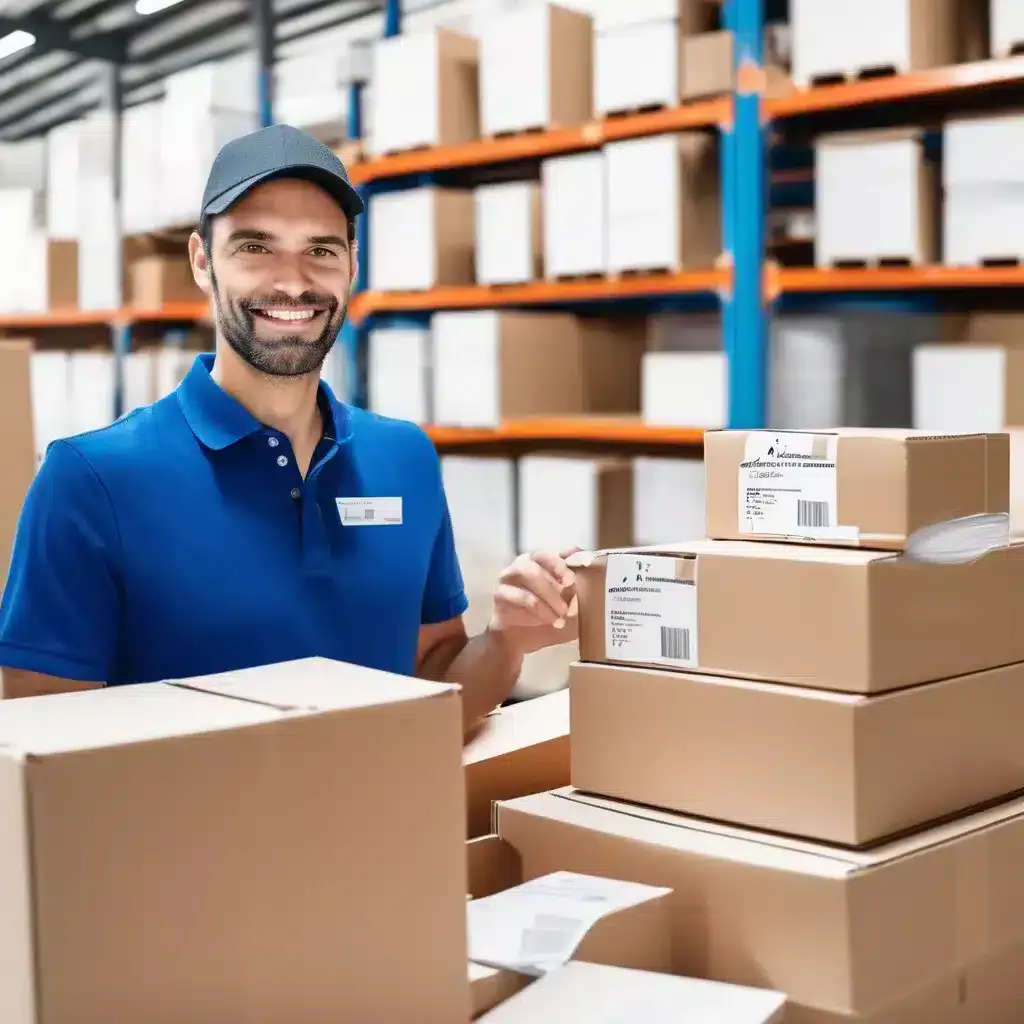
What are the impacts of this regulation on the Supply Chain?
GxP rules applied to the Supply Chain aim to ensure that products are manufactured, stored, and distributed under conditions that preserve their quality and safety, while ensuring regulatory compliance and traceability throughout the process. The impacts described in these paragraphs are not exhaustive. We have selected the most important ones, i.e. those that have the most impact on the tools, processes and organization of the Supply Chain of our pharmaceutical production site.
a. Introduction of materials & Qualification of suppliers
The development phase by the Manufacturing Science and Technology (MSAT) teams will make it possible to define the nomenclature of the product that will be manufactured by the site. Once this nomenclature has been defined (Bill Of Materials – BOM), the Supply Chain manages the introduction of the product on the site (known as “Material Introduction”). It is a question of coordinating the Manufacturing, Quality, Purchasing, MSAT teams to order and receive the raw materials defined in the nomenclature.
Before placing orders, suppliers are selected according to the price of materials, minimum quantities, delivery times, among other things. The objective is to optimize purchasing costs while ensuring the necessary stock levels to launch production. At this stage, as much information as possible is collected by the Supply Chain teams from the suppliers selected to draw up material specifications, a key element for product traceability.
The quality team ensures the qualification of suppliers in a more or less complex way depending on the GxP category (level) of the materials ordered. This GxP category is defined by subject. This is a decisive element for the rest of the introduction process and later for the traceability of the product. It is defined according to the end use of the raw material in the manufacturing process, as well as the type of material defined by the Supply Chain (chemical, process consumable, kanban consumable – cross process). This GxP category determines the complexity of managing the life of the material: from its introduction to its end of life, including its batch management. In other words, (and from a supply chain perspective only), it determines the level of accuracy of material traceability. A high GxP category will require complete quality control upon receipt of the material: documentary control (of delivery documents), laboratory control (sampling and analysis). The batch of this material will be blocked upon receipt and released for use in production by the quality department. He will be released only once all the tests have been carried out and assessed positive.
Once the selection of suppliers has been made, the qualification of these suppliers has been advanced, and the material specifications are finalized. These specifications are “bibles” of materials: they contain all the information about the product. General information (product code, supplier code, description, order unit of measure and alternative storage unit of measure) necessary for the laboratory and production (composition and other technical characteristics). They also contain the information necessary for logistics: packaging, size, weight, internal and external packaging, storage temperature. Finally, these specifications contain the information necessary for quality (presence of satellite samples, certificates of analysis and conformity (CoA, CoC). These specifications are approved and stored in an electronic document management system (eDMS). For the Supply Chain, they are critical because they will serve as a basis for the release of batches of incoming materials. In concrete terms, once the materials have been received, the batches are blocked upon receipt and released by the quality department. This release is a series of documentary, electronic (WMS) and physical controls carried out by the quality team. The specification serves as a basic document against which the quality compares the elements mentioned above. For example: the material description is the same on the physically received carton, in the warehouse management system in which the receipt is recorded (WMS), in the delivery documents provided by the delivery company (delivery note), and in the specification.
Of course, and this is an essential rule in a GxP environment, the processes of introducing and qualifying materials, qualifying suppliers, and releasing on receipt are processed, subject to good documentary practices and change management. This means that any deviation identified, or any required changes to the procedures related to these processes, are recorded in a Quality Management System (QMS). This recording will allow the modification of the procedure or work instruction related to the process that is being discarded or subject to a change.
b. Storage strategy, contracting with a service provider
Defining the storage strategy is decisive for the proper execution of material flows in compliance with GxP standards. Among others, we have selected 4 flows (described below) among the most decisive in the respect of GxP standards and to be defined with the storage strategy of our case study. In our article, and as in most pharmaceutical production sites, an external service provider is used to supplement the plant’s own storage. The service provider is obviously qualified by the country’s GxP certifying institutions.
Flow 1 – Good Receipt procedure
There are many solutions for defining the procedure for receiving materials. This must cover receipts at the storage service provider as well as receipts at the production site. Depending on the stock management systems used by the production site and the service provider, the stock management strategy between the service provider and the site may differ. The management strategy for batches of incoming materials will also be a structuring element of the storage strategy between the service provider and the factory. The acceptance procedure is rightly considered a key procedure for logistics. It is this procedure that defines the rules for receiving materials: quality and quantity controls, document collection, repalletizing on disinfected plastic pallets, system registration, temperature control, identification of potential deviations, formalization of reception (the reception checklist being a tool frequently used by logistics teams) etc. This procedure must also cover the rules for recording expiry dates, batch creation and thus the basis for the future traceability of the product.
Flow 2 – Sampling
It is key to define the sampling location of the highest GxP chemical feedstock in advance. As described above, these materials are subject to the strictest controls including sampling (or management of satellite samples) and analysis. The storage provider may be chosen as the sampling location if it complies with the GxP standards for this stream. If this is the case, this service must be covered by the approval or contract covering the service. Also, a procedure and work instructions will have to be drawn up to train the service provider in the requirements of the production site. The sampling plan is decisive for the site’s supply chain activities. This plan organizes the sampling activities, determines the quantities to be sampled and the number of containers received to be opened to carry out the sampling. These elements are variable and evolve over time because they depend on previous decisions on the use of other batches received for the same product. These elements impact the volumes to be ordered, the dates on which the products must be received and stored, but also the supply plan of the production line because sampling activities take time and must be integrated into the time frame for the availability of the products by the logistics team.
Flow 3 – Communication of Warehouse Management Systems (WMS Interfacing)
The storage provider has its own WMS tool but will offer more or less complex integration solutions with the WMS of our production site. Among many possibilities, it will be common to choose simplified stock management (at pallet level for example) from the service provider. On site, however, it is essential to choose stock management at the level of the Handling Unit to optimize the traceability of batches of materials that will be consumed in production. In this case, a solution commonly used in the industry and easy to deploy will be to give access (obviously to procedure and train) the WMS of the production site to its storage provider. The latter can then record the receipts in the site’s WMS, and create internal batches according to the site’s management rules (avoid the multiplication of batches between the supplier, the service provider and the site). If this solution is not possible, an interface between the 2 WMS will be necessary. In this case, sharing the item database will be necessary. This constraint (among others) will oblige the site and the service provider to harmonize the management rules, for example concerning the units of measure and the coding of items. The prerequisite for choosing the interfacing solution is to carefully study the technologies available at the service provider and on site, to review the safety constraints, and to align with the quality team to look for the most pragmatic solution that is best suited to the needs of the site. Storage providers in the pharmaceutical industry comply with standards and offer proven solutions together with other customers.
Flow 4 – Batch Management
The central element of material traceability is the batch. As in other industries, batch management is a requirement for compliance with GxP standards. This should allow for seamless traceability from the supplier to the patient. Upon first receipt of the supply batch of the material at the storage service provider or on the production site, the supplier batch number received, the expiry date and all the documents required by the acceptance and release procedures must be stored in an internal batch. This is the1st step in the long life of the material batch, which is so important to ensure a follow-up of the life of the product. The creation of the batch is also a prerequisite for sampling activities. Indeed, it is the internal batch number that will allow the test results of the samples taken to be traced. Finally, as explained above, the batch is the basic element for the release of materials after receipt: this is called a “batch file”. The receipt (and release) procedure will explain how the Supply Chain and in particular the Logistics teams will provide the information and documents necessary for the release of the batch by the Quality team. The lots will be subject to strict management of the articles of association (often electronic in the WMS). These statutes provide for the different cases of use and blocking of materials. Among other things, a distinction will be necessary between the blocked status (pending investigation for example) and the quarantine status (to be destroyed). The released status is the ultimate status that allows the material batch to be used for any inventory movement. This status, under certain strict conditions and a source of intense arbitration between the Supply Chain and Quality teams, can be supplemented by a conditionally released status allowing its use in a stock movement, subject to a future full release. The management of batch statuses is the responsibility of the Quality team, which means perfect integration with the logistics teams!
c. Release procedure
GxP standards require that each batch of raw materials, packaging, or finished products undergo rigorous quality control upon arrival. Samples are taken to verify compliance with the defined specifications. The release of a batch upon receipt requires complete documentation, including test results, storage conditions, and any other relevant information. According to GxP standards, each lot must be released for use or distribution by a qualified person. This person must ensure that the lot meets all regulatory requirements and quality standards before it is released. An effective traceability system must be in place to ensure that each batch can be traced throughout the manufacturing and distribution process.
Once received and created by Logistics, for the most critical GxP categories, batches of materials are said to be blocked. They cannot be used in order picking, inventory or any other stock movement. The logistics teams that have received the materials (at the external warehouse or at the production site) according to the receiving procedure, collect the required batch information. These will be delivery documents (delivery note, transport documents), certificates (available on the boxes, or on the supplier’s website), temperature recorders (in the case of refrigerated or frozen materials), acceptance documents following the system registration (receipt note). These elements will be made available (electronically or physically) to the quality team that will carry out the checks required by the release procedure. In the case of a critical GxP material requiring sampling, the test results will be required to release the batch of material definitively.
The release of the batch of material upon receipt is a strategic process for the rest of the product’s life. The site’s supply chain, via its logistics team, must take into account this release time used by the quality team in the planning of replenishments. The production plan can be put at risk if the reception and release stages are not mastered. The release process should be coordinated by the supply chain and prioritized based on the production plan, arrivals, the teams’ ability to collect required batch information and the laboratory team’s activities for sampling, and the time it takes to test materials (often performed by external providers).
We find these quality controls, and these sampling activities on receipt in other industries not subject to GxP standards. The specificity of these processes in the context of a GxP regulated environment is that batch traceability cannot be degraded. Batch information is a requirement to trace the life of the product in the event of an unwanted impact on the patient. Even if it may seem unnatural, it is the Supply Chain that must manage this activity (carried out by the Quality team) to ensure the continuation of the flow of materials and limit the impact on the production plan.
d. Transport validation
Each movement of material stock is subject to GxP standards. From its production by the supplier, to its consumption on the production line. The qualification of suppliers will include the qualification of the supplier’s production sites. It is common to consider transport from the supplier’s production site to the storage site (external or internal) included in the supplier’s qualification. The release of the incoming material will ensure the control of this transport on receipt. Stock transfers between the external warehouse and the production site in our example is a risk to the material. The validation of this transport must be included in the contract or approval signed between the production site and its storage provider. Otherwise, it will have to be subject to at least a formal risk assessment, if not a complete validation by the Supply Chain teams.
Validation is mainly concerned with temperature control during transport. This temperature is described in the material specification. It is often counterintuitive but required to consider transport at room temperature as having to be covered by this validation. It is much more obvious to validate the temperature control for refrigerated (2-8 degrees) and frozen (-20 degrees) products. Validating humidity controls requires more effort and is sometimes difficult to obtain from transport companies. Finally, certain materials such as the Working Cell Bank (WCB) or the shipment of the finished product will be subject to specific and thorough validation, their storage temperatures and therefore their conditions and means of transport being themselves specific.
e. Management of Units of Measure and labelling
Labeling is a GxP requirement (present in many industries) that has a significant impact (for example) on the workload of logistics teams. The objective of labeling is to be able to record by scanner (and therefore trace in the systems: ERP and MES) each handling unit used in the production process. Defining the labeling strategy is an important prerequisite, intimately linked to the management of units of measure.
Properly defining the units of measure requires integrating all the departments handling the products into the thinking. The flows of reception, storage, order preparation, consumption in production and shipments must be formalized and validated in the corresponding procedures. The external service provider must be included in the reflection because it is, for the majority of products, the first player in the scope of our case study. The supplier is also obviously integrated, being the initial source of information.
The labeling workload can quickly become substantial. Despite the technology available, it is still a very manual, time-consuming and error-prone activity. Without having checked, it would be interesting to establish a statistic on the number of observations relating to labelling during the audits of the inspection bodies.
To define the most optimal strategy, several labelling steps may be considered depending on where the product is stored. The further away the product is from its place of consumption, the more labelling can be done at the level of the external packaging of the product, or even at the level of the pallet.
f. Other key processes
Among the other processes that are decisive for compliance with GxP standards, we could have selected the drafting of procedures, their periodic reviews and the training of staff. Supplier replenishment planning is also impacted, for example in the event of a supplier shortage and/or when there is a need to source an alternative to a product, and its necessary integration with the material introduction process. Equipment & Systems Qualification is a world of its own, and our production facility’s supply chain may have the most GxP design, but no product can be used on the production line (in GxP mode) until the storage areas and equipment and handling equipment are qualified. The ERP and/or WMS tool is also subject to validation managed by the CSV (Computer Science Validation) Quality teams. As the Supply Chain is obviously a customer of the qualification and validation activities in this case, it will have to ensure the proper execution of the qualification and requalification activities necessary for its logistics processes by coordinating the various actors.
As described in the previous chapters, raw material sampling has a significant impact on the processes, tools and organization of the site’s supply chain. Indeed, this activity requires having received the materials, and is a prerequisite for the use of materials by production (and therefore for a prerequisite for downstream logistics activities).
Finally, the planning of production deliveries and the management of Supply Chain activities could also be subjects in their own right, as the impact of the processes previously described, structured by the GxP requirements, determine the management of warehouse activities and the management of the Supply Chain of our production site in general.
Ready to transform your supply chain?
Contact us today to schedule a call and discover how we can optimize your operations.
How to implement (or upgrade) your GxP Supply Chain?
In a intense context of starting a production site, one of our points of contact was a (very) experienced quality expert. He had an impressive list of situations he had to deal with, the most critical of which was a contamination of a production line. With a lot of hindsight, at the dawn of his career in a pharmaceutical factory (in Switzerland), he did us the honor of sharing his observation. To do this, he used a simple image. We hope here not to distort his words (knowing, knowing his humor, that he won’t blame us if he recognizes himself!).
In summary, his words looked like this: “Building (or upgrading) a GxP Supply Chain is comparable to building a house: the foundations must be solid, it requires a range of trades, only experts can do it, the orchestration of interventions is decisive, an experienced project manager must be in charge, only then will the owner be able to live in his house on the expected date and evolve in it according to his desires and needs in complete serenity”.
The first step in laying this solid foundation must be a precise description of the processes for managing the flow of goods and people. These processes will help you ask yourself the right questions and define your GxP supply chain strategy. The choice of equipment and systems must be the subject of an in-depth study and their qualification/validation must be piloted in order to integrate with operational activities.
Processes integrated with other departments (in particular material introduction, batch release, sampling) must be anticipated and prioritized to finalize the definition of supply chain processes. The functionalities of the ERP or WMS system must be aligned with these processes described (and must sometimes be restrictive in the definition of these: “don’t reinvent the wheel”). Operational activities should be organized by functional flows (avoid silos): for example, batch release activity, including sampling activity, should be fully integrated with production plan scheduling. “Compliance”, in other words, the level of training of teams in GxP requirements must be high enough for the Supply Chain teams and quality teams to operate as teams from the 1st subject introduced. The management of material master data and their continuous introduction (in the event of new sourcing, or the opening of a new production line) should not be neglected under any circumstances: it will be at the center of the field at all times. The logistics teams will be sized taking into account the labelling activities (upon receipt and/or during order preparation). The process of delivering materials into production (as well as returns) will be given special attention (in particular the stages of transfer of responsibility). Critical products (WCBs, finished products, products stored in refrigerated or frozen) will be covered by instructions and procedures in their own right.
The shipping activity will be evaluated specifically according to the desired scope and defined in the analysis phase. Finally, defining expert points of contact for Supply Chain GxP and Compliance will relieve the operational teams and ensure the consistency of GxP records (deviations, change control, etc.) and documentation. These resources are scarce because they must know the Supply Chain processes and integrate the responsiveness they require. At the same time, they must bring their value by integrating GxP requirements (documentation, training, deviation and change management, preparation for audits and inspections, etc.) in the most efficient way possible into the processes, tools and organization of the Supply Chain team.
As we can see, the experts to set up a GxP Supply Chain (or bring it up to standard) are multidisciplinary (Logistics, procurement, quality, production, etc.).
As a Supply Chain consulting firm, our experience in Supply Chain and Lean management in a Pharmaceutical environment, our profiles as Supply Chain Transformation project managers, our technical expertise in Logistics and Warehouse Management, our knowledge of GxP Supply Chain best practices, our field experience as an orchestra (and execution) leader of several GxP Supply Chains (full or partial), allow us to offer our services to build or upgrade your GxP Supply Chain. We offer our services in the role of architect, project management or execution, in the context of opening a production site, commercial supply chain, introducing a new product (and a new production line), remediation following an audit, studying a storage area or finding a storage service provider, and finally upgrading ERP and WMS.
Conclusion
When you read this article, you have probably thought that the processes described are finally the ones you find in your industry. If you’re a professional in the GxP environment, you may have thought that the structuring GxP requirements described could have been others. We would love to hear from you, but we are confident enough to say that yes, the complexity of GxP standards comes in their application and that supply chain processes in the pharmaceutical industry are ultimately rather classic compared to other industries. The examples of document management and labeling confirm this statement: the complexity of these processes comes from the GxP requirements!
From experience, if the basics of the processes described in this article are not put in place in accordance with the GxP requirements from the start, it will be difficult to bring them up to standard. External support can catalyze strategic thinking, bring an external perspective on your organization, a new dynamic, as well as current best practices, to help you overcome the obstacles that prevent you from calmly facing your audits and delivering your products at the expected level of quality. SuCh Consulting offers these activities, in addition to an experienced team that will work collaboratively with you to provide this support.
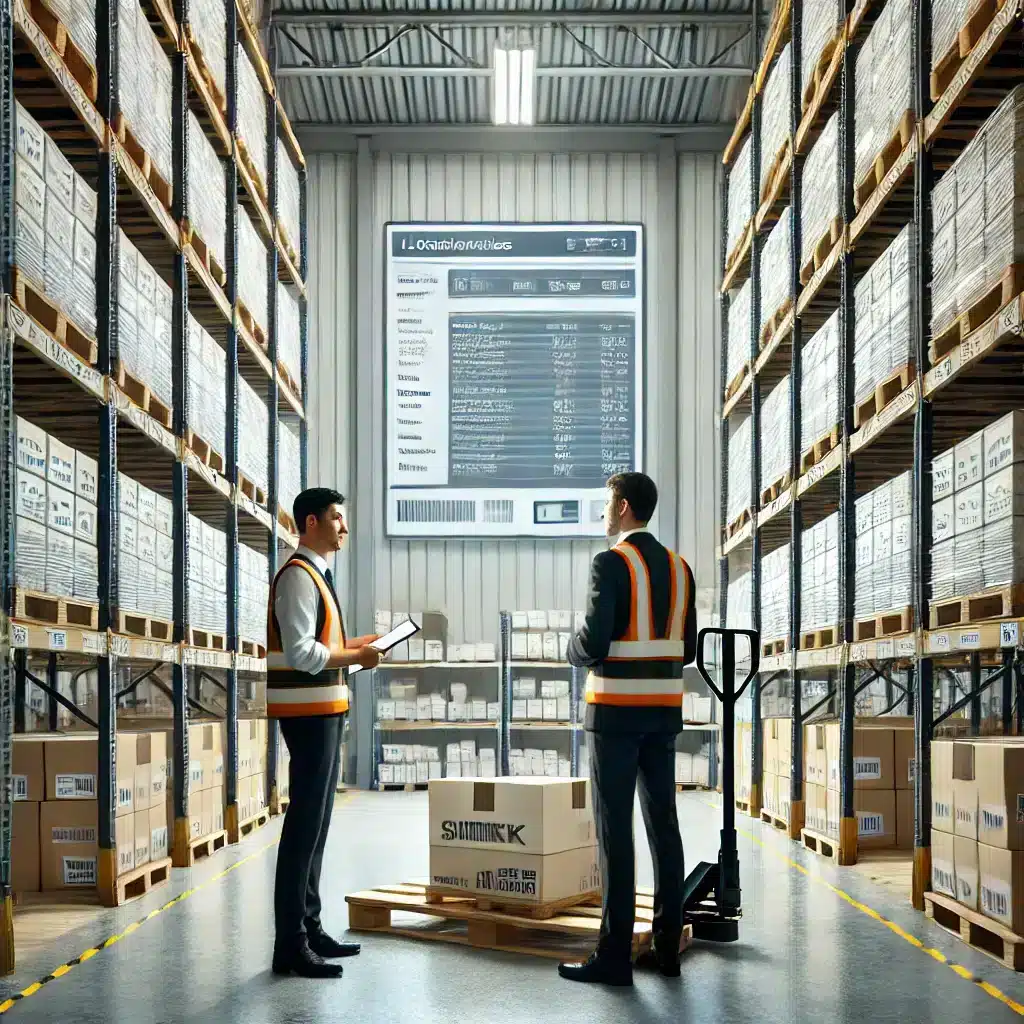